মেডিকেল ডায়াগনস্টিক সরঞ্জামের জন্য নেমা ২৩ (৫৭ মিমি) হাইব্রিড বল স্ক্রু স্টেপার মোটর ১.৮° স্টেপ অ্যাঙ্গেল ৪ লিড ওয়্যার
মেডিকেল ডায়াগনস্টিক সরঞ্জামের জন্য নেমা ২৩ (৫৭ মিমি) হাইব্রিড বল স্ক্রু স্টেপার মোটর ১.৮° স্টেপ অ্যাঙ্গেল ৪ লিড ওয়্যার
নেমা ২৩ (৫৭ মিমি) হাইব্রিড স্টেপার মোটর, বাইপোলার, ৪-লিড, বল স্ক্রু, কম শব্দ, দীর্ঘ জীবন, উচ্চ কর্মক্ষমতা, সিই এবং RoHS সার্টিফাইড।
বড় লোড ক্ষমতা, ছোট কম্পন, কম শব্দ, দ্রুত গতি, দ্রুত প্রতিক্রিয়া, মসৃণ অপারেশন, দীর্ঘ জীবন, উচ্চ অবস্থান নির্ভুলতা (±0.005 মিমি পর্যন্ত)
বিবরণ
পণ্যের নাম | ৫৭ মিমি হাইব্রিড বল স্ক্রু স্টেপার মোটর |
মডেল | VSM57BSHSM সম্পর্কে |
আদর্শ | হাইব্রিড স্টেপার মোটর |
ধাপ কোণ | ১.৮° |
ভোল্টেজ (V) | ২.৩ / ৩ / ৩.১ / ৩.৮ |
বর্তমান (A) | ৩/৪ |
প্রতিরোধ (ওহম) | ০.৭৫ / ১ / ০.৭৮ / ০.৯৫ |
আবেশ (মিলিহার্জ) | ২.৫ / ৪.৫ / ৩.৩ / ৪.৫ |
সীসার তার | 4 |
মোটর দৈর্ঘ্য (মিমি) | ৪৫/৫৫/৬৫/৭৫ |
পরিবেষ্টিত তাপমাত্রা | -২০ ℃ ~ +৫০ ℃ |
তাপমাত্রা বৃদ্ধি | সর্বোচ্চ ৮০ হাজার। |
ডাইইলেকট্রিক শক্তি | সর্বোচ্চ ১ এমএ @ ৫০০ ভোল্ট, ১ কেজি হার্জ, ১ সেকেন্ড। |
অন্তরণ প্রতিরোধের | ১০০MΩ সর্বনিম্ন @৫০০Vdc |
সার্টিফিকেশন
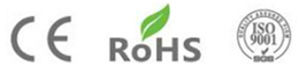
বৈদ্যুতিক পরামিতি:
মোটর আকার | ভোল্টেজ /পর্যায় (ভি) | বর্তমান /পর্যায় (ক) | প্রতিরোধ /পর্যায় (Ω) | আবেশ /পর্যায় (মিলিহার্জ) | সংখ্যা সীসার তার | রোটার জড়তা (গ্রাম.সেমি2) | মোটর ওজন (ছ) | মোটর দৈর্ঘ্য এল (মিমি) |
57 | ২.৩ | 3 | ০.৭৫ | ২.৫ | 4 | ১৫০ | ৫৮০ | 45 |
57 | 3 | 3 | 1 | ৪.৫ | 4 | ৩০০ | ৭১০ | 55 |
57 | ৩.১ | 4 | ০.৭৮ | ৩.৩ | 4 | ৪০০ | ৮৮০ | 65 |
57 | ৩.৮ | 4 | ০.৯৫ | ৪.৫ | 4 | ৪৮০ | ৯৫০ | 75 |
VSM57BSHSM স্ট্যান্ডার্ড বহিরাগত মোটর রূপরেখা অঙ্কন:
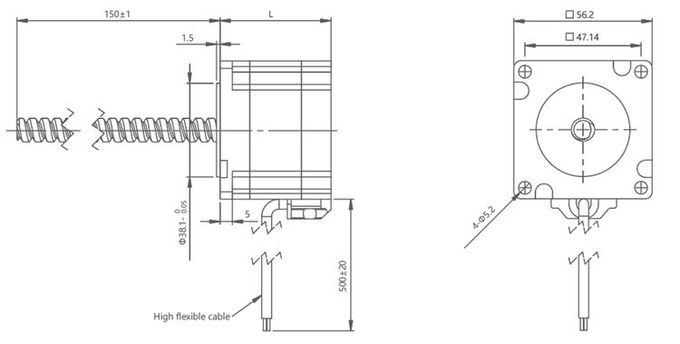
নোট:
লিড স্ক্রু দৈর্ঘ্য কাস্টমাইজ করা যেতে পারে
সীসা স্ক্রুর শেষে কাস্টমাইজড মেশিনিং কার্যকর
আরও বল স্ক্রু স্পেসিফিকেশনের জন্য আমাদের সাথে যোগাযোগ করুন।
VSM57BSHSMBall nut 1202 রূপরেখা অঙ্কন:
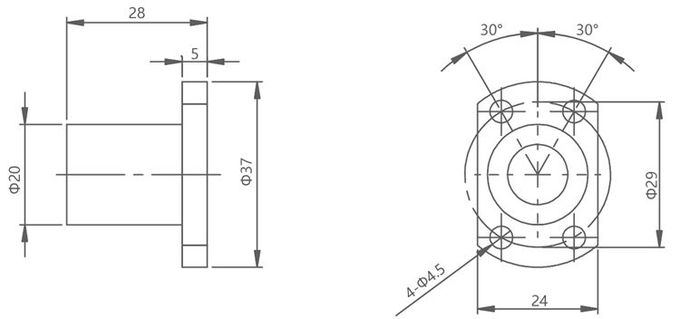
VSM57BSHSMBall nut 1205 রূপরেখা অঙ্কন:
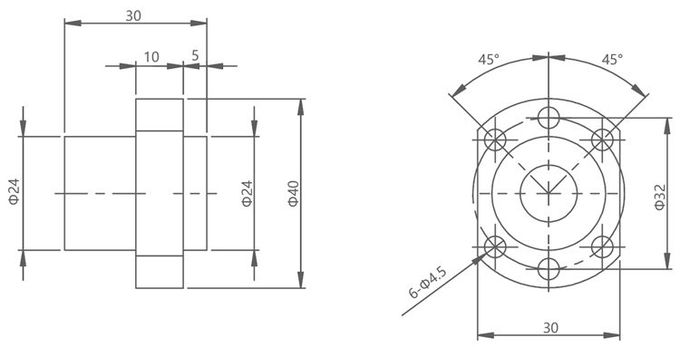
VSM57BSHSMBall nut 1210 রূপরেখা অঙ্কন:
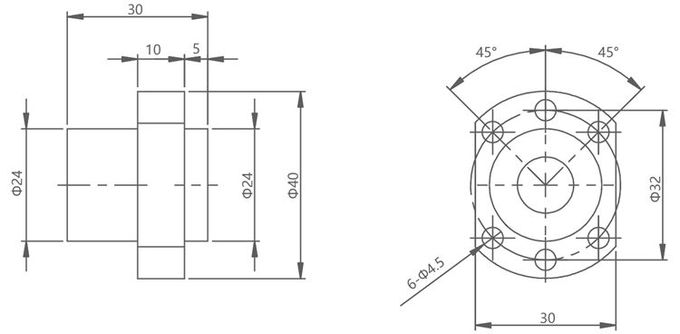
VSM57BSHSMBall nut 1210 রূপরেখা অঙ্কন:
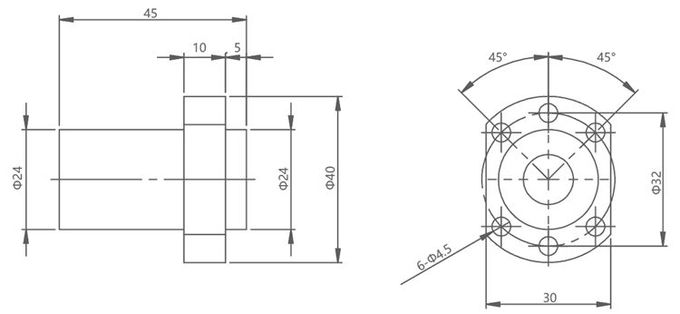
গতি এবং থ্রাস্ট বক্ররেখা
৫৭ সিরিজ ৪৫ মিমি মোটর দৈর্ঘ্যের বাইপোলার চপার ড্রাইভ
১০০% কারেন্ট পালস ফ্রিকোয়েন্সি এবং থ্রাস্ট কার্ভ
৫৭ সিরিজ ৫৫ মিমি মোটর দৈর্ঘ্যের বাইপোলার চপার ড্রাইভ
১০০% কারেন্ট পালস ফ্রিকোয়েন্সি এবং থ্রাস্ট কার্ভ
সীসা (মিমি) | রৈখিক বেগ (মিমি/সেকেন্ড) | |||||||
2 | 2 | 4 | 6 | 8 | 10 | 12 | 14 | 16 |
5 | 5 | 10 | 15 | 20 | 25 | 30 | 35 | 40 |
10 | 10 | 20 | 30 | 40 | 50 | 60 | 70 | 80 |
পরীক্ষার অবস্থা:চপার ড্রাইভ, কোন র্যাম্পিং নেই, অর্ধেক মাইক্রো-স্টেপিং, ড্রাইভ ভোল্টেজ 40V
৫৭ সিরিজ ৬৫ মিমি মোটর দৈর্ঘ্যের বাইপোলার চপার ড্রাইভ
১০০% কারেন্ট পালস ফ্রিকোয়েন্সি এবং থ্রাস্ট কার্ভ
৫৭ সিরিজ ৭৫ মিমি মোটর দৈর্ঘ্যের বাইপোলার চপার ড্রাইভ
১০০% কারেন্ট পালস ফ্রিকোয়েন্সি এবং থ্রাস্ট কার্ভ
সীসা (মিমি) | রৈখিক বেগ (মিমি/সেকেন্ড) | |||||||
2 | 2 | 4 | 6 | 8 | 10 | 12 | 14 | 16 |
5 | 5 | 10 | 15 | 20 | 25 | 30 | 35 | 40 |
10 | 10 | 20 | 30 | 40 | 50 | 60 | 70 | 80 |
পরীক্ষার অবস্থা:চপার ড্রাইভ, কোন র্যাম্পিং নেই, অর্ধেক মাইক্রো-স্টেপিং, ড্রাইভ ভোল্টেজ 40V
প্রয়োগের ক্ষেত্র:
চিকিৎসা রোগ নির্ণয়ের সরঞ্জাম:৫৭ মিমি হাইব্রিড বল স্ক্রু স্টেপার মোটরগুলি মেডিকেল ডায়াগনস্টিক সরঞ্জাম যেমন ইমেজ স্ক্যানার, সিটি স্ক্যানার, এক্স-রে সরঞ্জাম, এমআরআই যন্ত্র ইত্যাদিতে ব্যবহার করা যেতে পারে। তাদের উচ্চ নির্ভুলতা অবস্থান নিয়ন্ত্রণ এবং স্থিতিশীলতা মেডিকেল ইমেজ অর্জন এবং প্রক্রিয়াকরণের সময় সুনির্দিষ্ট চলাচল এবং অবস্থান নির্ধারণকে সক্ষম করে।
জীবন বিজ্ঞানের যন্ত্রপাতি:জীবন বিজ্ঞান গবেষণা এবং পরীক্ষা-নিরীক্ষায়, ৫৭ মিমি হাইব্রিড বল স্ক্রু স্টেপার মোটরগুলি স্বয়ংক্রিয় তরল হ্যান্ডলিং সিস্টেম, উচ্চ-থ্রুপুট স্ক্রিনিং সরঞ্জাম, কোষ সংস্কৃতি ডিভাইস, জিন সিকোয়েন্সার এবং আরও অনেক কিছুতে ব্যবহৃত হয়। এই মোটরগুলির উচ্চ নির্ভুলতা এবং নির্ভরযোগ্যতা পরীক্ষামূলক সরঞ্জামগুলিতে সুনির্দিষ্ট গতি এবং অবস্থান নিয়ন্ত্রণের চাহিদা মেটাতে সক্ষম করে।
রোবোটিক্স:৫৭ মিমি হাইব্রিড বল স্ক্রু স্টেপার মোটর রোবোটিক্সে জয়েন্ট ড্রাইভ, রোবোটিক আর্ম মোশন এবং প্রিসিশন পজিশনিংয়ের জন্য ব্যাপকভাবে ব্যবহৃত হয়। রোবোটিক্স অ্যাপ্লিকেশনগুলিতে প্রিসিশন গতি এবং নিয়ন্ত্রণের চাহিদা মেটাতে এই মোটরগুলি উচ্চ টর্ক, উচ্চ রেজোলিউশন এবং কম শব্দ দ্বারা চিহ্নিত করা হয়।
লেজার সরঞ্জাম:৫৭ মিমি হাইব্রিড বল স্ক্রু স্টেপার মোটর লেজার সরঞ্জামগুলিতে ফোকাস অ্যাডজাস্টমেন্ট, প্যানিং টেবিল এবং অপটিক্যাল পাথ নিয়ন্ত্রণের মতো কাজের জন্য ব্যবহার করা যেতে পারে। এর উচ্চ-নির্ভুল অবস্থান নিয়ন্ত্রণ এবং স্থিতিশীলতা এটিকে লেজার রশ্মির সুনির্দিষ্ট ফোকাসিং এবং অবস্থান নির্ধারণ করতে সক্ষম করে।
বিশ্লেষণাত্মক যন্ত্র:বিভিন্ন ধরণের ল্যাবরেটরি বিশ্লেষণাত্মক যন্ত্রে, 57 মিমি হাইব্রিড বল স্ক্রু স্টেপার মোটরগুলি স্বয়ংক্রিয় নমুনা প্রক্রিয়াকরণ, নমুনা খাওয়ানোর ব্যবস্থা, তরল ক্রোমাটোগ্রাফ, গ্যাস ক্রোমাটোগ্রাফ ইত্যাদিতে ব্যবহার করা যেতে পারে। এই মোটরগুলির উচ্চ-নির্ভুলতা গতি এবং স্থিতিশীল কর্মক্ষমতা পরীক্ষাগার বিশ্লেষণের নির্ভুলতা এবং দক্ষতা উন্নত করতে গুরুত্বপূর্ণ ভূমিকা পালন করে।
সেমিকন্ডাক্টর এবং ইলেকট্রনিক উৎপাদন সরঞ্জাম:৫৭ মিমি হাইব্রিড বল স্ক্রু স্টেপার মোটরগুলি সেমিকন্ডাক্টর এবং ইলেকট্রনিক উৎপাদন সরঞ্জামগুলিতে নির্ভুল অবস্থান এবং অটোমেশন নিয়ন্ত্রণের জন্য ব্যবহৃত হয়। উদাহরণস্বরূপ, এগুলি সেমিকন্ডাক্টর চিপ পরীক্ষার সরঞ্জাম, প্যাকেজিং মেশিন, সারফেস মাউন্ট প্রযুক্তি, মুদ্রিত সার্কিট বোর্ড উত্পাদন এবং অন্যান্য ক্ষেত্রে উচ্চ-গতি, উচ্চ-নির্ভুলতা এবং নির্ভরযোগ্য গতি নিয়ন্ত্রণ প্রদানের জন্য ব্যবহার করা যেতে পারে।
অ-মানক অটোমেশন সরঞ্জাম এবং বিভিন্ন ধরণের অটোমেশন সরঞ্জাম:৫৭ মিমি হাইব্রিড বল স্ক্রু স্টেপার মোটরগুলি বিভিন্ন ধরণের অ-মানক অটোমেশন সরঞ্জাম এবং স্বয়ংক্রিয় উৎপাদন লাইনের জন্য উপযুক্ত। এগুলি পজিশনিং সরঞ্জাম, স্বয়ংক্রিয় সমাবেশ সিস্টেম, প্যাকেজিং সরঞ্জাম, মুদ্রণ যন্ত্রপাতি, টেক্সটাইল সরঞ্জাম ইত্যাদিতে ব্যবহার করা যেতে পারে। এগুলি বিভিন্ন ক্ষেত্রে অটোমেশনের চাহিদা মেটাতে সুনির্দিষ্ট অবস্থান নিয়ন্ত্রণ এবং নির্ভরযোগ্য গতি কর্মক্ষমতা প্রদান করে।
সুবিধা
উচ্চ টর্ক-টু-ইনার্শিয়া অনুপাত:হাইব্রিড বল স্ক্রু স্টেপার মোটরগুলির টর্ক-টু-ইনার্শিয়া অনুপাত উচ্চ, যার অর্থ তারা তাদের আকার এবং ওজনের তুলনায় উল্লেখযোগ্য টর্ক আউটপুট প্রদান করতে পারে। এটি রোবোটিক্স, সিএনসি মেশিন এবং অটোমেশন সিস্টেমের মতো কম্প্যাক্ট ফর্ম ফ্যাক্টরে উচ্চ টর্কের প্রয়োজন এমন অ্যাপ্লিকেশনগুলির জন্য এগুলিকে আদর্শ করে তোলে।
উচ্চ ত্বরণ এবং মন্দা:এই মোটরগুলি দ্রুত ত্বরণ এবং গতি হ্রাস করতে সক্ষম, যা দ্রুত এবং সুনির্দিষ্ট চলাচলের সুযোগ করে দেয়। রটারের কম জড়তা এবং উচ্চ টর্ক আউটপুট মোটরটিকে নিয়ন্ত্রণ সংকেতগুলিতে দ্রুত সাড়া দিতে সক্ষম করে, যার ফলে দ্রুত স্টার্ট-স্টপ সময় এবং সামগ্রিক সিস্টেমের কর্মক্ষমতা উন্নত হয়।
মসৃণ মাইক্রোস্টেপিং:হাইব্রিড বল স্ক্রু স্টেপার মোটরগুলি মাইক্রোস্টেপিং অপারেশনের জন্য উপযুক্ত, যা সূক্ষ্ম রেজোলিউশন এবং মসৃণ গতি নিয়ন্ত্রণের অনুমতি দেয়। মাইক্রোস্টেপিং প্রতিটি পূর্ণ পদক্ষেপকে ছোট ছোট উপ-পদক্ষেপে বিভক্ত করে, ধাপের আকার হ্রাস করে এবং কম্পন, শব্দ এবং অনুরণন প্রভাব হ্রাস করে। এই বৈশিষ্ট্যটি বিশেষ করে এমন অ্যাপ্লিকেশনগুলিতে উপকারী যেখানে মসৃণ এবং সুনির্দিষ্ট গতি প্রয়োজন, যেমন 3D প্রিন্টার এবং লিনিয়ার পজিশনিং সিস্টেম।
কম প্রতিক্রিয়া:এই মোটরগুলিতে বল স্ক্রু প্রক্রিয়া ব্যাকল্যাশ কমাতে সাহায্য করে, যা রটার এবং লোডের মধ্যে প্লে বা ক্লিয়ারেন্স। কম ব্যাকল্যাশ সঠিক অবস্থান এবং পুনরাবৃত্তিযোগ্যতা নিশ্চিত করে, কারণ দিক পরিবর্তন করার সময় বা চলাচল বিপরীত করার সময় ন্যূনতম হারানো গতি থাকে। পিক-অ্যান্ড-প্লেস মেশিন এবং অপটিক্যাল সিস্টেমের মতো সুনির্দিষ্ট এবং পুনরাবৃত্তিযোগ্য অবস্থানের প্রয়োজন এমন অ্যাপ্লিকেশনগুলির জন্য এটি অত্যন্ত গুরুত্বপূর্ণ।
উচ্চ গতিশীল প্রতিক্রিয়া:হাইব্রিড স্টেপার মোটর এবং বল স্ক্রু মেকানিজমের সংমিশ্রণ উচ্চ গতিশীল প্রতিক্রিয়া প্রদান করে, যার অর্থ মোটর দ্রুত এবং সঠিকভাবে নিয়ন্ত্রণ সংকেতের পরিবর্তনগুলি অনুসরণ করতে পারে। এই প্রতিক্রিয়াশীলতা এমন অ্যাপ্লিকেশনগুলির জন্য অপরিহার্য যেখানে গতি, দিক বা অবস্থানের দ্রুত পরিবর্তন জড়িত, যেমন উচ্চ-গতির মেশিনিং এবং গতিশীল গতি নিয়ন্ত্রণ ব্যবস্থা।
তাপীয় দক্ষতা:হাইব্রিড বল স্ক্রু স্টেপার মোটরগুলি ভাল তাপ দক্ষতার জন্য ডিজাইন করা হয়েছে, যা অপারেশন চলাকালীন কার্যকর তাপ অপচয়কে অনুমতি দেয়। এটি অতিরিক্ত গরম হওয়া রোধ করতে সাহায্য করে এবং দীর্ঘস্থায়ী ব্যবহারের সময় বা কঠিন অ্যাপ্লিকেশনের সময়ও স্থিতিশীল মোটর কর্মক্ষমতা নিশ্চিত করে।
সাশ্রয়ী সমাধান:হাইব্রিড বল স্ক্রু স্টেপার মোটরগুলি উচ্চ নির্ভুলতা এবং টর্কের প্রয়োজন এমন অ্যাপ্লিকেশনগুলির জন্য একটি সাশ্রয়ী সমাধান প্রদান করে। আরও জটিল এবং ব্যয়বহুল সার্ভো মোটর সিস্টেমের তুলনায়, হাইব্রিড স্টেপার মোটরগুলি কর্মক্ষমতা, খরচ এবং ব্যবহারের সহজতার মধ্যে ভারসাম্য প্রদান করে। এগুলি প্রায়শই এমন অ্যাপ্লিকেশনগুলির জন্য একটি পছন্দসই পছন্দ যেখানে খরচ একটি গুরুত্বপূর্ণ বিষয়, গুণমান এবং কর্মক্ষমতার সাথে আপস না করে।
মোটর নির্বাচনের প্রয়োজনীয়তা:
► চলাচল/মাউন্টিং দিক
► লোডের প্রয়োজনীয়তা
►স্ট্রোকের প্রয়োজনীয়তা
► শেষ যন্ত্রের প্রয়োজনীয়তা
►নির্ভুলতার প্রয়োজনীয়তা
►এনকোডার প্রতিক্রিয়ার প্রয়োজনীয়তা
►ম্যানুয়াল সমন্বয়ের প্রয়োজনীয়তা
►পরিবেশগত প্রয়োজনীয়তা
উৎপাদন কর্মশালা
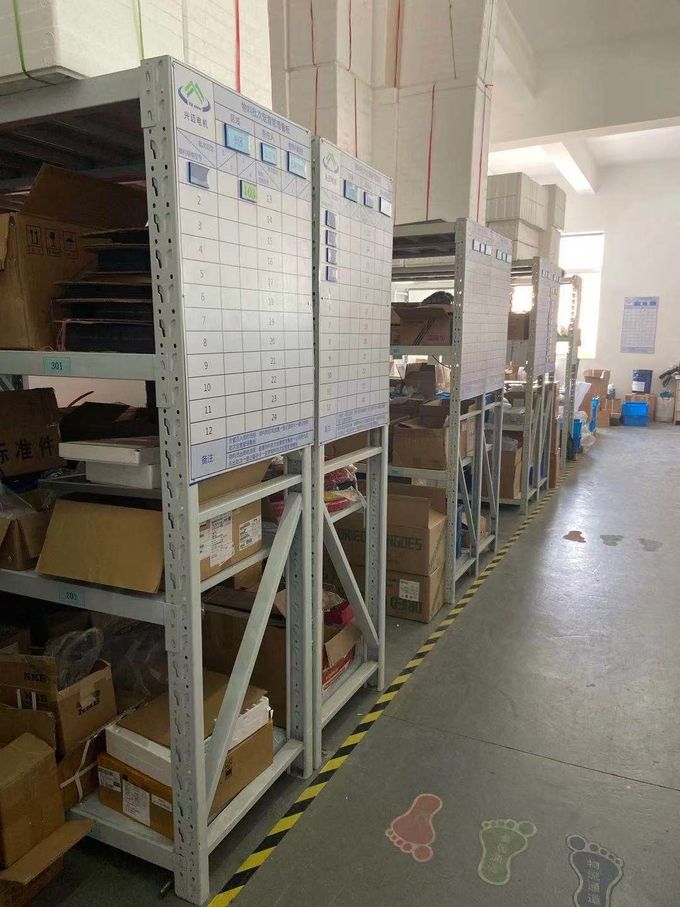
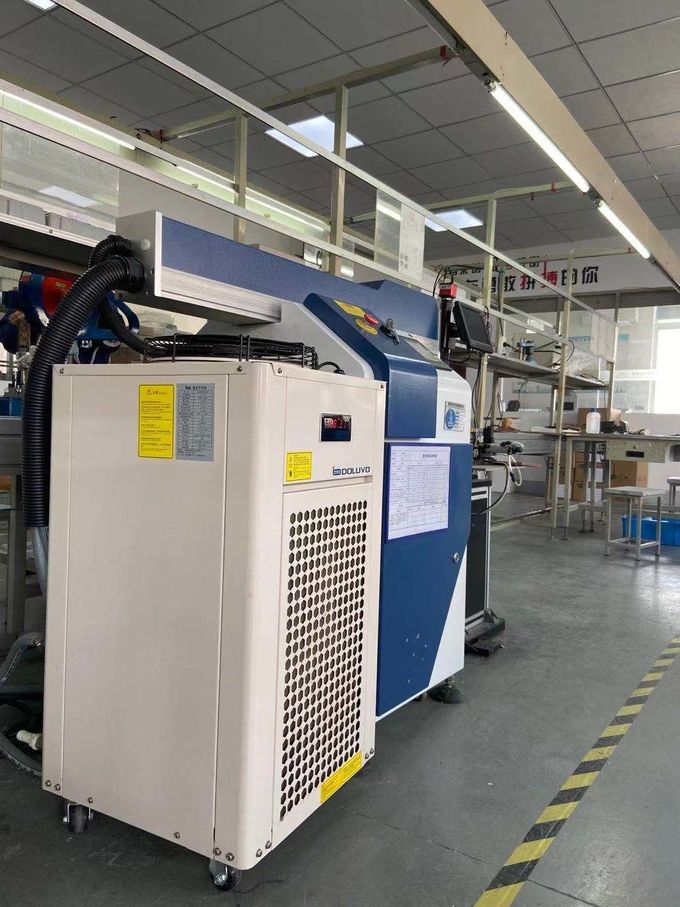